For wastewater treatment plants, sludge management is an ongoing responsibility that can also carry significant costs. An anaerobic digester can be implemented as part of the water treatment process, reducing the odor, total mass, organic content, and pathogen content of the wastewater. It can also be incorporated to process the sludge produced during aerobic digestion, reducing the overall mass quantity by 5-40% by converting the organic material into biogas.
With the digester treating your sludge, disposal costs are often greatly reduced. Energy costs to run the treatment plant can be expensive, but these costs can be offset by utilizing the biogas produced to generate renewable electricity and heat. Excess biogas can be used for additional revenue by selling electricity or upgraded RNG to the grid. Installing a biogas upgrading system introduces diverse revenue streams to your operation. Produced biogas can be used directly to generate electricity, upgraded for injection to the natural gas grid or upgraded and compressed/liquified to vehicle fuel.
BIOFerm Solutions for Wastewater
Anaerobic Digester
Improve your wastewater treatment and/or mange the sludge effluent while producing biogas that can be used for onsite heat & power.
Gas Upgrading
Process your biogas to valuable pipeline-quality renewable natural gas (RNG).
Combined System
Utilize any of your facility’s waste streams as feedstock for anaerobic digestion, producing biogas that is then upgraded to renewable natural gas (RNG).
Featured project – Anaerobic digestion
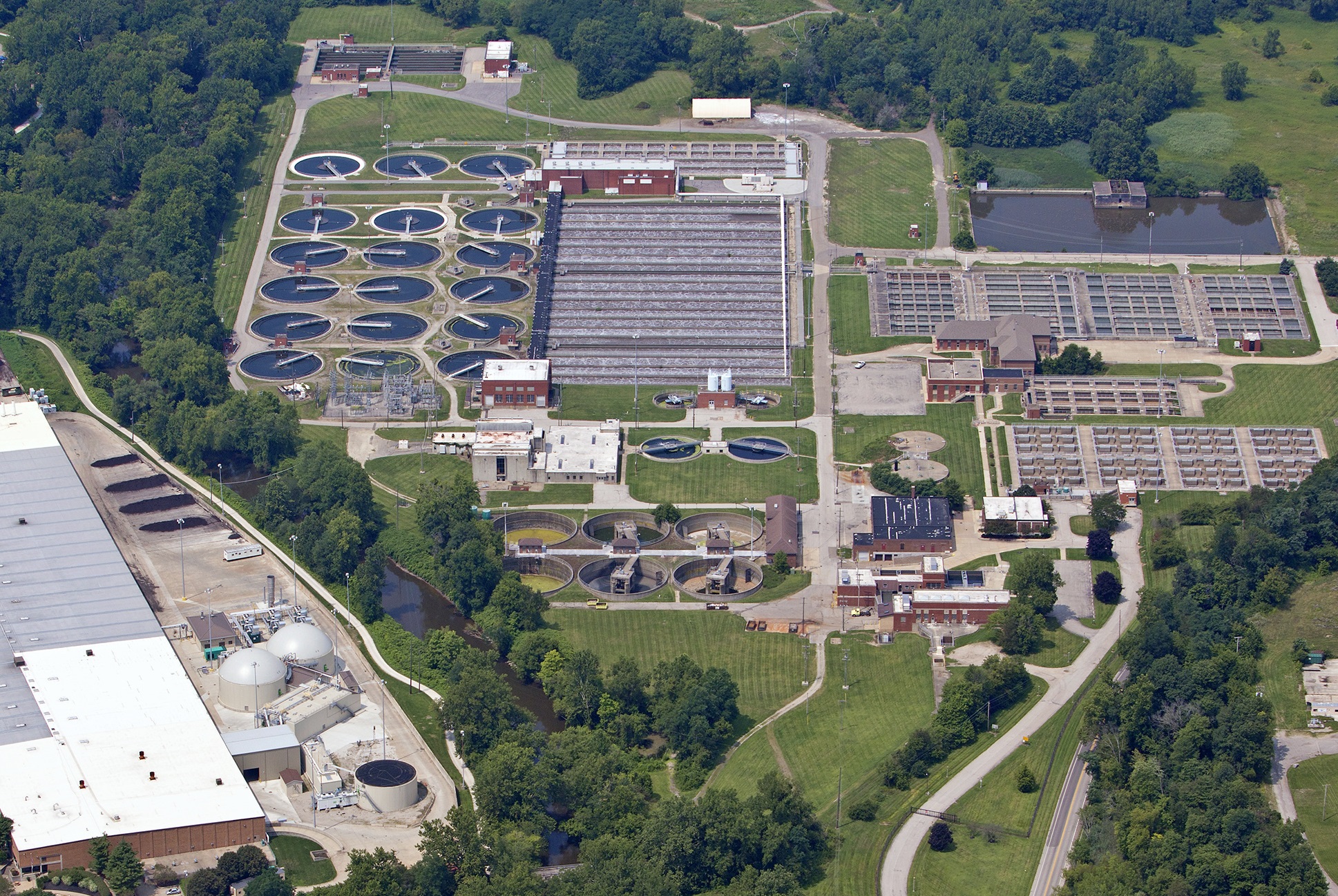
As Phase I, BIOFerm constructed a continuously-stirred tank & plug-flow anaerobic digestion system in 2007 to process wastewater sewage sludge from the city of Akron, Ohioʼs municipal treatment plant. This facility was built as a joint venture between the City of Akron and KB BioEnergy.
In 2013, a Phase II expansion was added which allows the digesters to now process 100% of the facilityʼs sewage sludge, generating additional renewable energy. Phase I handled about 7,000 dry tons of biosolids per year, and Phase II processes more than double that with 15,000 tons per year.